In the wake of a workplace incident, an incentive program sounds like an appealing solution to improve workplace safety. It worked for your children, why not your employees?
Unfortunately, incentive programs that offer tangible rewards for safety compliance, often lead to safety cultures that foster under-reporting. No one wants to be the teammate who thwarts everyone from that cash incentive, right? A culture like this doesn’t actually improve workplace safety and, in fact, may even hinder and erode trust.
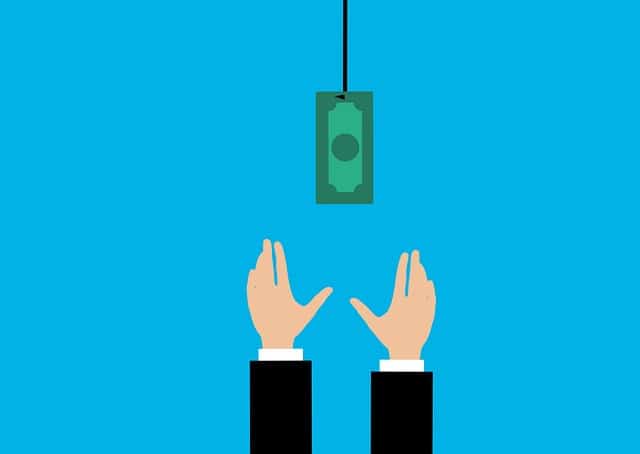
A good alternative to traditional incentive programs is to recognize and reward good safety practices. Ultimately, you can’t buy a good safety culture. You’ve got to cultivate it through everyday operations. Achieve the culture you want with actions that reinforce your company’s commitment to safety and improvement.
Do:
- Encourage safe behavior with safety lunches, raffles or on the spot recognition
- Track and incorporate in your company’s leading indicators into the recognition program (more on that below)
Don't:
-
- Go over the top with expensive prizes and monetary rewards
- Focus on tangible rewards
- Implement a point related system
If you’re incentivizing, do it around leading indicators.
Leading indicators are “proactive, preventive, and predictive measures that provide information about the effective performance of your safety and health activities,” according to OSHA. The number of safety audits conducted in the last 12 months is an example of a leading indicator. Lagging indicators are previously recorded numbers (e.g. number of injuries in the last 12 months). This type of indicator can be helpful for retrospective review but should not be incentivized because they penalize employee mistakes and incidents. Incentive programs that recognize leading indicators reward good behavior.
Examples of leading indicators:
- Safety audits conducted
- Job hazard analyses completed
- Trainings completed
- Toolbox talks held
- Near misses reported
Examples of lagging indicators:
- Recordable injuries
- Incidents reported
- Amount of equipment damage
- Near misses penalized
Here is an example of how an incentive program can backfire:
The Widget Factory recently had a recordable injury. To work towards improving their safety program, they implemented an incentive program. Every employee will receive a new work jacket at the end of the year if there are no more incidents.
Employee are thrilled and now expect the jacket. However, they feel pressure from their coworkers to hide near misses and incidents. Jeff, a newer Widget Factory employee, slips and sprains his ankle in the factory. Instead of reporting his injury, he walks it off and tells his supervisor that he was injured off the clock. The Widget Factory is now open to legal liability due to under reporting.
Here is an example of safety incentives done right:
The Thingamajig Factory has an effective safety program but wants to improve overall culture. They’ve recently noticed that only certain foremen are complying with company safety policies and procedures, and others taking shortcuts. The company encourages the foremen to participate more with toolbox talks, job hazard analyses and safety audits. When participation improves, the company provides lunch to the employees to express appreciation. Employees feel recognized, valued and the Thingamajig Factory’s safety culture improves.
OSHA’s stance on safety incentive programs:
Incentive programs fall under the Recordkeeping Standard in OSHA 1904.35. OSHA as released a statement explaining that incentive programs can be effective if they fall under the following requirements:
- “The program focuses on involvement in the safety and health management system.
- The employees are not incentivized into a “rate-based” program.
- The program does not discourage reporting in the workplace.”